Minipod style tripod for near bottom current and wave measurements ready for deployment.
Coastal and Estuarine Dynamics Project Active
Coastal and Estuarine Dynamics Project exists to support ocean, coastal and estuarine research. The staff have a broad set of skills; from instrument design and development to all forms of work at sea to software development and data management. The team has successfully deployed and recovered more than 1000 data collection platforms for research in the last 30 years.
Research Themes
The Coastal and Estuarine Dynamics Group's research, projects, and equipment.
The U.S. Geological Survey (USGS) Coastal and Estuarine Dynamics Project, part of the USGS Woods Hole Coastal and Marine Science Center, provides operational support for studies of coastal ocean circulation and sediment transport. The Coastal and Estuarine Dynamics Project staff design, fabricate, deploy, and recover a variety of instrumented platforms for research. It has capabilities in engineering, software development, project management, data acquisition, data processing and data archiving. Instrument measurement quality assessments, interface design, and development of novel housings are all examples of the engineering tasks routinely completed. The Coastal and Estuarine Dynamics Project maintains a diverse pool of high-quality oceanographic instruments, and develop new techniques to improve or modify existing sensors and systems. Field experiments are conducted in estuarine, coastal, and continental shelf regions. Oceanographic moorings, tripods and other platforms are deployed at water depths ranges from less than a meter to more than a thousand meters.
The Coastal and Estuarine Dynamics Project team members have extensive experience in collecting and managing oceanographic data from deep water to near shore environments. They support research projects carried out by scientists at the USGS Woods Hole Coastal and Marine Science Center and their colleagues, with assistance to other programs as resources allow.
The data collected are typically comprised of measurements from sensors deployed in arrays at fixed locations. These time-series observations are used in studies of regional circulation and sediment transport processes in estuaries, marshes, beach regions and in the coastal ocean. The observation periods range from a few days to more than a year. Since 1975, the Coastal and Estuarine Dynamics Project has deployed over 1000 separate platforms in support of field research programs.
An extensive software system has been developed and maintained to decode, process, edit, display, archive and analyze the oceanographic data collected. This system uses Matlab® and python programs to output files in EPIC-compliant NetCDF format. CF-Compliant NetCDF files are also created and are available at [http://cfconventions.org] and the Oceanographic Time-Series Database.
Time series observations collected throughout the U.S. Exclusive Economic Zone (E.E.Z.) by the group since 1975 are managed, archived and distributed to collaborators, other investigators, and the public over the World Wide Web as part of the U.S. Geological Survey Oceanographic Time-Series Database (see http://stellwagen.er.usgs.gov). File downloads and access via OPeNDAP are possible from the page describing each experiment.
Below are other science projects associated with this project.
Coastal and Estuarine Dynamics- Equipment
Estuarine Processes, Hazards, and Ecosystems
Coastal and Estuarine Dynamics- Projects
Coastal and Estuarine Dynamics - Engineering
Below are data or web applications associated with this project.
Grain-Size Analysis Data From Sediment Samples in Support of Oceanographic and Water-Quality Measurements in the Nearshore Zone of Matanzas Inlet, Florida, 2018
Water level measurements collected in West Falmouth Harbor, MA, 2016: U.S. Geological Survey data release
Water level measurements collected in West Falmouth Harbor, MA, 2017
Water samples in support of oceanographic and water-quality measurements in Chincoteague Bay, Maryland and Virginia, 2014-15, U.S. Geological Survey Field Activity 2014-048-FA
Below are multimedia items associated with this project.
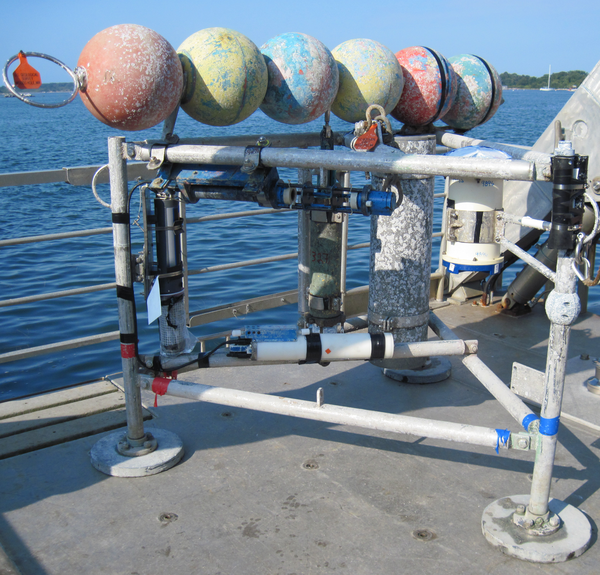
Minipod style tripod for near bottom current and wave measurements ready for deployment.
Divers prepare patterns of known targets for verification of sonar resolution.
Divers prepare patterns of known targets for verification of sonar resolution.
A flow tripod (taller, right) and sonar tripod (smaller, left) at the dock before being loaded onto a ship and taken to a site off Fire Island for deployment.
A flow tripod (taller, right) and sonar tripod (smaller, left) at the dock before being loaded onto a ship and taken to a site off Fire Island for deployment.
Deployment of an instrumented quadrapod off Martha’s Vineyard, November 2014.
Deployment of an instrumented quadrapod off Martha’s Vineyard, November 2014.
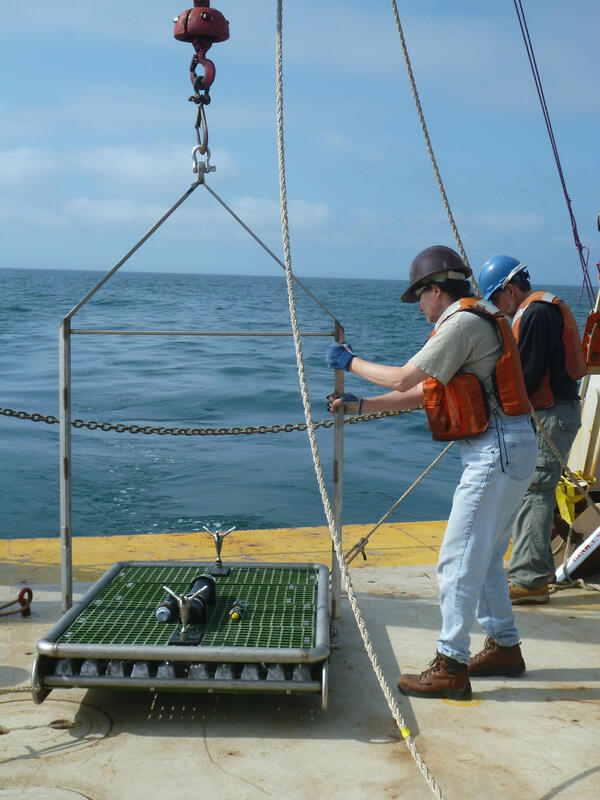
Marinna Martini prepares to deploy a NIMBBLE from the R/V Connecticut south of Martha's Vineyard
Marinna Martini prepares to deploy a NIMBBLE from the R/V Connecticut south of Martha's Vineyard
USGS technicians prepare a sediment trap to sample the sea floor off Cape Hatteras.
USGS technicians prepare a sediment trap to sample the sea floor off Cape Hatteras.
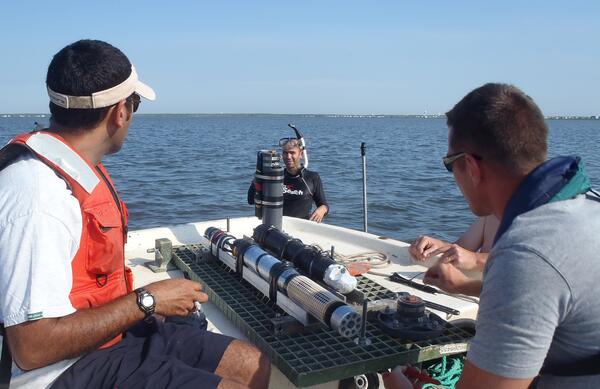
Investigators prepare to place a Shallow Water Irradience Platform (SWIP) at a site in Barnegat Bay, NJ.
Investigators prepare to place a Shallow Water Irradience Platform (SWIP) at a site in Barnegat Bay, NJ.
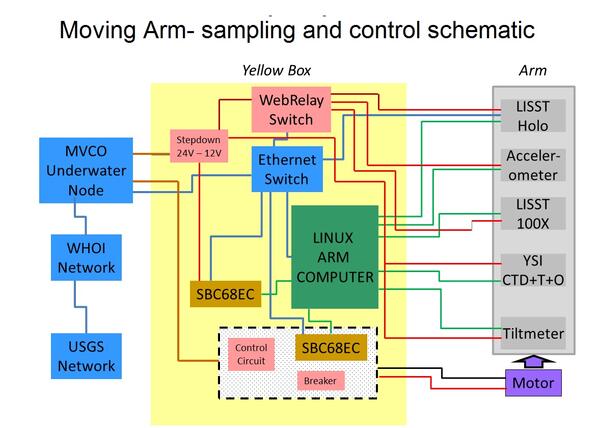
Schematic of system designed to control movement and logging of data collected by the Moving Arm Tripod at Martha's Vineyard Coastal Observatory in 2011.
Schematic of system designed to control movement and logging of data collected by the Moving Arm Tripod at Martha's Vineyard Coastal Observatory in 2011.
Electronics for controlling the moving arm in the open pressure housing.
Electronics for controlling the moving arm in the open pressure housing.
USGS researchers deploying an instrumented minipod South of Fire Island, NY.
USGS researchers deploying an instrumented minipod South of Fire Island, NY.
Woods Hole Coastal and Marine Science Center's Ellyn Montgomery (right) on the helipad of the Canadian Coast Guard Vessel Louis St. Laurent returning from an ice reconnaissance flight as part of a joint study mapping the foot of the continental slope in the Arctic Ocean in 2008
Woods Hole Coastal and Marine Science Center's Ellyn Montgomery (right) on the helipad of the Canadian Coast Guard Vessel Louis St. Laurent returning from an ice reconnaissance flight as part of a joint study mapping the foot of the continental slope in the Arctic Ocean in 2008
Below are publications associated with this project.
Documentation of the U.S. Geological Survey Oceanographic time-series measurement database
Summary of oceanographic and water-quality measurements offshore of Matanzas Inlet, Florida, 2018
Summary of oceanographic and water-quality measurements in Chincoteague Bay, Maryland and Virginia, 2014–15
Spectral wave dissipation by submerged aquatic vegetation in a back-barrier estuary
Summary of oceanographic and water-quality measurements in Barnegat Bay, New Jersey, 2014–15
Quantification of storm-induced bathymetric change in a back-barrier estuary
Summary of oceanographic measurements for characterizing light attenuation and sediment resuspension in the Barnegat Bay-Little Egg Harbor Estuary, New Jersey, 2013
Summary of oceanographic and water-quality measurements in Rachel Carson National Wildlife Refuge, Wells, Maine, in 2013
Coastal Change Processes Project data report for oceanographic observations near Fire Island, New York, February through May 2014
Water-level and wave measurements in the Chandeleur Islands, Louisiana, 2012 and 2013
Coastal Change Processes Project data report for observations near Fire Island, New York, January to April 2012
Studying seafloor bedforms using autonomous stationary imaging and profiling sonars
Summary of oceanographic and water-quality measurements near the Blackwater National Wildlife Refuge, Maryland, 2011
Coastal and Estuarine Dynamics Project exists to support ocean, coastal and estuarine research. The staff have a broad set of skills; from instrument design and development to all forms of work at sea to software development and data management. The team has successfully deployed and recovered more than 1000 data collection platforms for research in the last 30 years.
Research Themes
The Coastal and Estuarine Dynamics Group's research, projects, and equipment.
The U.S. Geological Survey (USGS) Coastal and Estuarine Dynamics Project, part of the USGS Woods Hole Coastal and Marine Science Center, provides operational support for studies of coastal ocean circulation and sediment transport. The Coastal and Estuarine Dynamics Project staff design, fabricate, deploy, and recover a variety of instrumented platforms for research. It has capabilities in engineering, software development, project management, data acquisition, data processing and data archiving. Instrument measurement quality assessments, interface design, and development of novel housings are all examples of the engineering tasks routinely completed. The Coastal and Estuarine Dynamics Project maintains a diverse pool of high-quality oceanographic instruments, and develop new techniques to improve or modify existing sensors and systems. Field experiments are conducted in estuarine, coastal, and continental shelf regions. Oceanographic moorings, tripods and other platforms are deployed at water depths ranges from less than a meter to more than a thousand meters.
The Coastal and Estuarine Dynamics Project team members have extensive experience in collecting and managing oceanographic data from deep water to near shore environments. They support research projects carried out by scientists at the USGS Woods Hole Coastal and Marine Science Center and their colleagues, with assistance to other programs as resources allow.
The data collected are typically comprised of measurements from sensors deployed in arrays at fixed locations. These time-series observations are used in studies of regional circulation and sediment transport processes in estuaries, marshes, beach regions and in the coastal ocean. The observation periods range from a few days to more than a year. Since 1975, the Coastal and Estuarine Dynamics Project has deployed over 1000 separate platforms in support of field research programs.
An extensive software system has been developed and maintained to decode, process, edit, display, archive and analyze the oceanographic data collected. This system uses Matlab® and python programs to output files in EPIC-compliant NetCDF format. CF-Compliant NetCDF files are also created and are available at [http://cfconventions.org] and the Oceanographic Time-Series Database.
Time series observations collected throughout the U.S. Exclusive Economic Zone (E.E.Z.) by the group since 1975 are managed, archived and distributed to collaborators, other investigators, and the public over the World Wide Web as part of the U.S. Geological Survey Oceanographic Time-Series Database (see http://stellwagen.er.usgs.gov). File downloads and access via OPeNDAP are possible from the page describing each experiment.
Below are other science projects associated with this project.
Coastal and Estuarine Dynamics- Equipment
Estuarine Processes, Hazards, and Ecosystems
Coastal and Estuarine Dynamics- Projects
Coastal and Estuarine Dynamics - Engineering
Below are data or web applications associated with this project.
Grain-Size Analysis Data From Sediment Samples in Support of Oceanographic and Water-Quality Measurements in the Nearshore Zone of Matanzas Inlet, Florida, 2018
Water level measurements collected in West Falmouth Harbor, MA, 2016: U.S. Geological Survey data release
Water level measurements collected in West Falmouth Harbor, MA, 2017
Water samples in support of oceanographic and water-quality measurements in Chincoteague Bay, Maryland and Virginia, 2014-15, U.S. Geological Survey Field Activity 2014-048-FA
Below are multimedia items associated with this project.
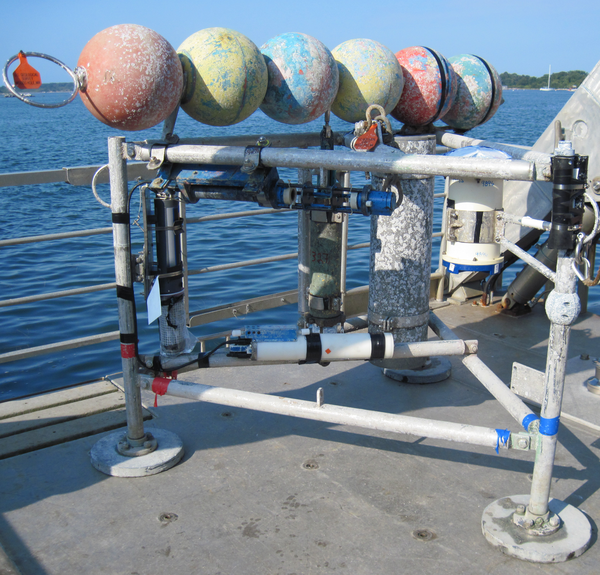
Minipod style tripod for near bottom current and wave measurements ready for deployment.
Minipod style tripod for near bottom current and wave measurements ready for deployment.
Divers prepare patterns of known targets for verification of sonar resolution.
Divers prepare patterns of known targets for verification of sonar resolution.
A flow tripod (taller, right) and sonar tripod (smaller, left) at the dock before being loaded onto a ship and taken to a site off Fire Island for deployment.
A flow tripod (taller, right) and sonar tripod (smaller, left) at the dock before being loaded onto a ship and taken to a site off Fire Island for deployment.
Deployment of an instrumented quadrapod off Martha’s Vineyard, November 2014.
Deployment of an instrumented quadrapod off Martha’s Vineyard, November 2014.
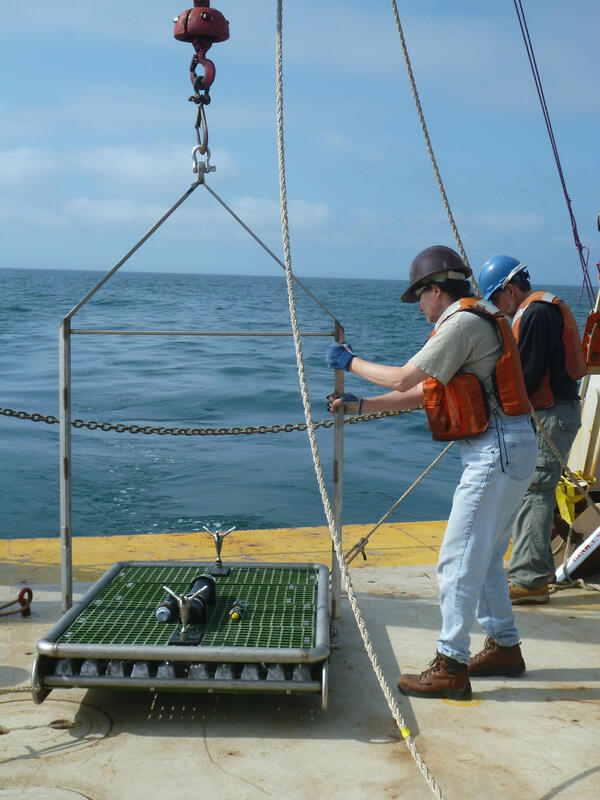
Marinna Martini prepares to deploy a NIMBBLE from the R/V Connecticut south of Martha's Vineyard
Marinna Martini prepares to deploy a NIMBBLE from the R/V Connecticut south of Martha's Vineyard
USGS technicians prepare a sediment trap to sample the sea floor off Cape Hatteras.
USGS technicians prepare a sediment trap to sample the sea floor off Cape Hatteras.
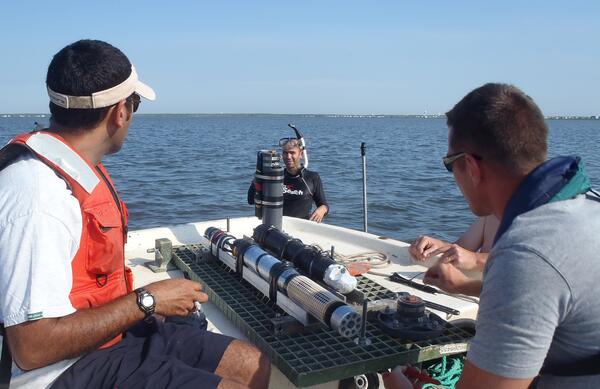
Investigators prepare to place a Shallow Water Irradience Platform (SWIP) at a site in Barnegat Bay, NJ.
Investigators prepare to place a Shallow Water Irradience Platform (SWIP) at a site in Barnegat Bay, NJ.
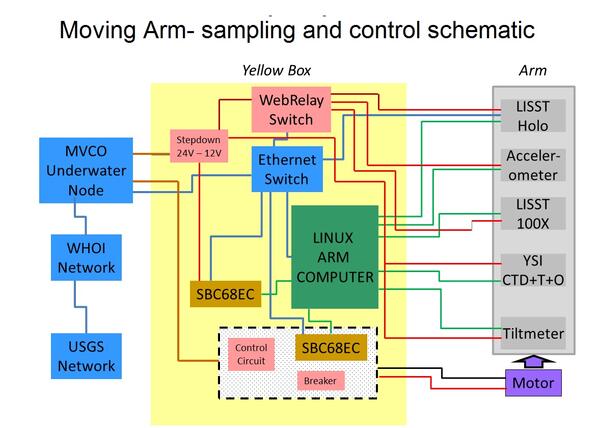
Schematic of system designed to control movement and logging of data collected by the Moving Arm Tripod at Martha's Vineyard Coastal Observatory in 2011.
Schematic of system designed to control movement and logging of data collected by the Moving Arm Tripod at Martha's Vineyard Coastal Observatory in 2011.
Electronics for controlling the moving arm in the open pressure housing.
Electronics for controlling the moving arm in the open pressure housing.
USGS researchers deploying an instrumented minipod South of Fire Island, NY.
USGS researchers deploying an instrumented minipod South of Fire Island, NY.
Woods Hole Coastal and Marine Science Center's Ellyn Montgomery (right) on the helipad of the Canadian Coast Guard Vessel Louis St. Laurent returning from an ice reconnaissance flight as part of a joint study mapping the foot of the continental slope in the Arctic Ocean in 2008
Woods Hole Coastal and Marine Science Center's Ellyn Montgomery (right) on the helipad of the Canadian Coast Guard Vessel Louis St. Laurent returning from an ice reconnaissance flight as part of a joint study mapping the foot of the continental slope in the Arctic Ocean in 2008
Below are publications associated with this project.